Risk Management in Production Planning
- Kayla Tyree
- Jul 18, 2023
- 5 min read
Updated: Apr 15
By Kayla Tyree
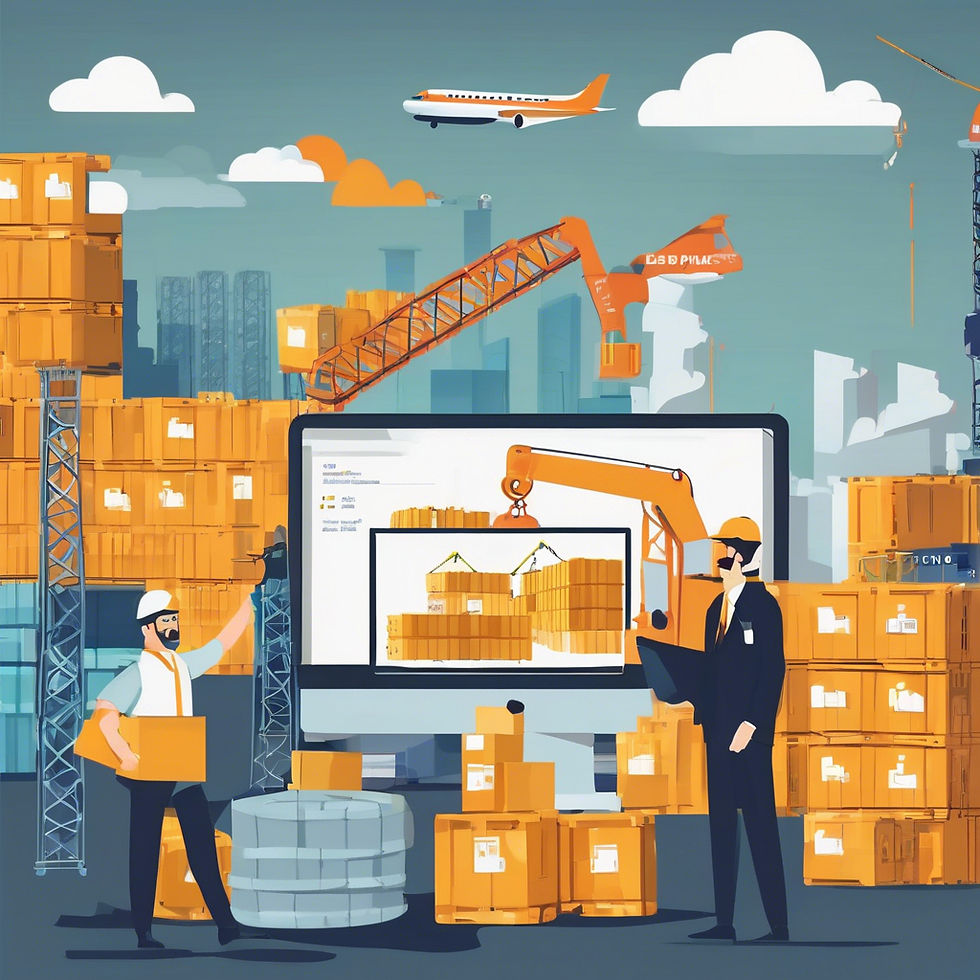
Production planning is a critical aspect of supply chain management in the manufacturing process as it involves determining what, when, and how much to produce to meet customer demand while considering various operational and logistical factors. Risk management plays a crucial role in ensuring the smooth functioning of the supply chain and mitigating potential disruptions.
From establishing raw materials and labor needs to demand forecasting, production planning helps ensure processes run smoothly and efficiently. It assists in determining production targets, necessary resources, and the overall production schedule. A properly constructed production plan can help to achieve optimal efficiency and customer satisfaction by aligning production capabilities with customer demand. In generating any successful production plan, however, the risks must be considered. Risks have the capability to disrupt entire supply chains, causing delays, cost increases, and leading to dissatisfied customers. Risk management helps the production planning process by identifying these potential risks and assessing strategies to mitigate and manage them effectively. It involves a comprehensive evaluation of all factors both internal and external that could play a role in hindering production capability. Here we will explore the essential steps and key concepts related to risk management.
Risk Identification
The first step in risk management is to identify the various potential risk sources that could cause issues within the production planning process. These could include any number of factors such as labor problems, lack of materials, faulty machines, rush orders, and quality issues. In order to garner a diverse perspective, it is important to gather information from the various relevant groups involved in the production process. This means engaging with production teams, supply chain managers, and suppliers to help identify risks that may have otherwise been overlooked. The idea here is to compile a comprehensive list of all potential risks that pose a threat towards the production planning process. This can be completed using various techniques such as brainstorming, historical data analysis, or SWOT analysis.
Risk Analysis
After identifying possible risks, the next step is to prioritize each risk by conducting an assessment to judge their likelihood and potential impact. One can begin determining the level of importance of each risk through the application of quantitative or qualitative risk assessment techniques and the use of risk simulations. This process can be made easier using a risk matrix, a tool that offers a visual representation of risk analysis and categorizes each risk based on potential impact and probability of occurrence. By assigning a numerical or descriptive value to each risk, it creates the opportunity to focus on those of a higher priority so that contingency resources can be allocated efficiently. This is a crucial step in the risk management process, as it will aid in determining the level of preparedness apportioned to each risk.
Risk Planning
After deciding on the seriousness of each risk, it is then necessary to begin creating appropriate plans based on risk severity. There are several potential responses one could take depending on the type and level of risk. First, you could aim towards avoiding the risk by changing the production plan. This is an optimal choice as it helps to eliminate risks entirely, however, it can be difficult to accomplish. The second option is to simply mitigate risks by implementing protective measures. This is similar to avoidance although it involves less changing of the production plan as a whole. Additionally, there is the potential to reduce risk by contractually shifting it to another party. This involves utilizing your relationships and creating contracts that transfer liability to your contractors, subcontractors, vendors or consumers. Finally, you could choose to simply accept the possibility of a risk but do nothing except be prepared to accept the consequences in case of disruptions. This can be an easier approach but it must be calculated whether it would be the most cost effective option. One important aspect to consider here is that it will be necessary to create multiple contingency plans should the measures originally put in place to reduce risk ultimately fail. Creating many options for yourself such as maintaining safety stock, having backup suppliers, and generating multiple transportation routes are all helpful in ensuring the mitigation of supply chain disruptions.
Risk Monitoring
The final step in the risk management process is to establish monitoring systems for ongoing review of contingency plan outcomes. By performing regular assessments of the progress of these strategies, expected outcomes can be compared to actual outcomes so that updates and adjustments may be made to the plans as necessary. The use of tools such as key performance indicators (KPIs), risk registers, and real time data collection systems can all be helpful in tracking the effectiveness of various risk mitigation strategies. This ability to track data in real time allows production planners to receive early alerts of potential disruptions so that the appropriate responses may be made.
Additional Strategies for Risk Mitigation
Though these steps are the basis for any good risk mitigation plan, there are various strategies that may be employed to further aid and streamline the process. First, refining communication channels in addition to establishing strong connections and relationships with suppliers can help to greatly reduce the risk of supplier disruptions. Second, standardizing the production process assists in reducing waste and bottlenecks in order to improve efficiency as a whole. Third, using forecasting software to ensure an accurate demand forecast can aid in optimizing resource allocation to lower the risk of under or over production. Finally, the adoption of techniques such as demand driven inventory replenishment strategies and just-in-time (JIT) inventory systems can be beneficial in creating a balance between carrying costs and consumer demand. Both the application of these methods and the implementation of proper risk mitigation tactics can help to give your business a proper competitive edge.
Conclusion
Risk management plays a pivotal role in production planning by allowing organizations to analyze and mitigate risks that could disrupt operations. The optimization of production efficiency, cost reduction, and customer satisfaction can all be achieved within an organization through the application of risk management systems. In a world as volatile and complex as it so currently is, it is crucial to prepare for risk whenever possible. Since risk management is a continual process, regularly reviewing and reevaluating the implementation of risk management systems is critical in ensuring its vitality. Embracing the ability to learn and grow from past mistakes and work towards continuous improvement is an important way to ensure that the best possible practices are administered throughout an organization.
ASCI specializes in helping businesses like yours to address supply chain management challenges. Visit our website to learn more and to arrange for a free consultation.
Comments